Maintaining Investment Balance in Industry 4.0
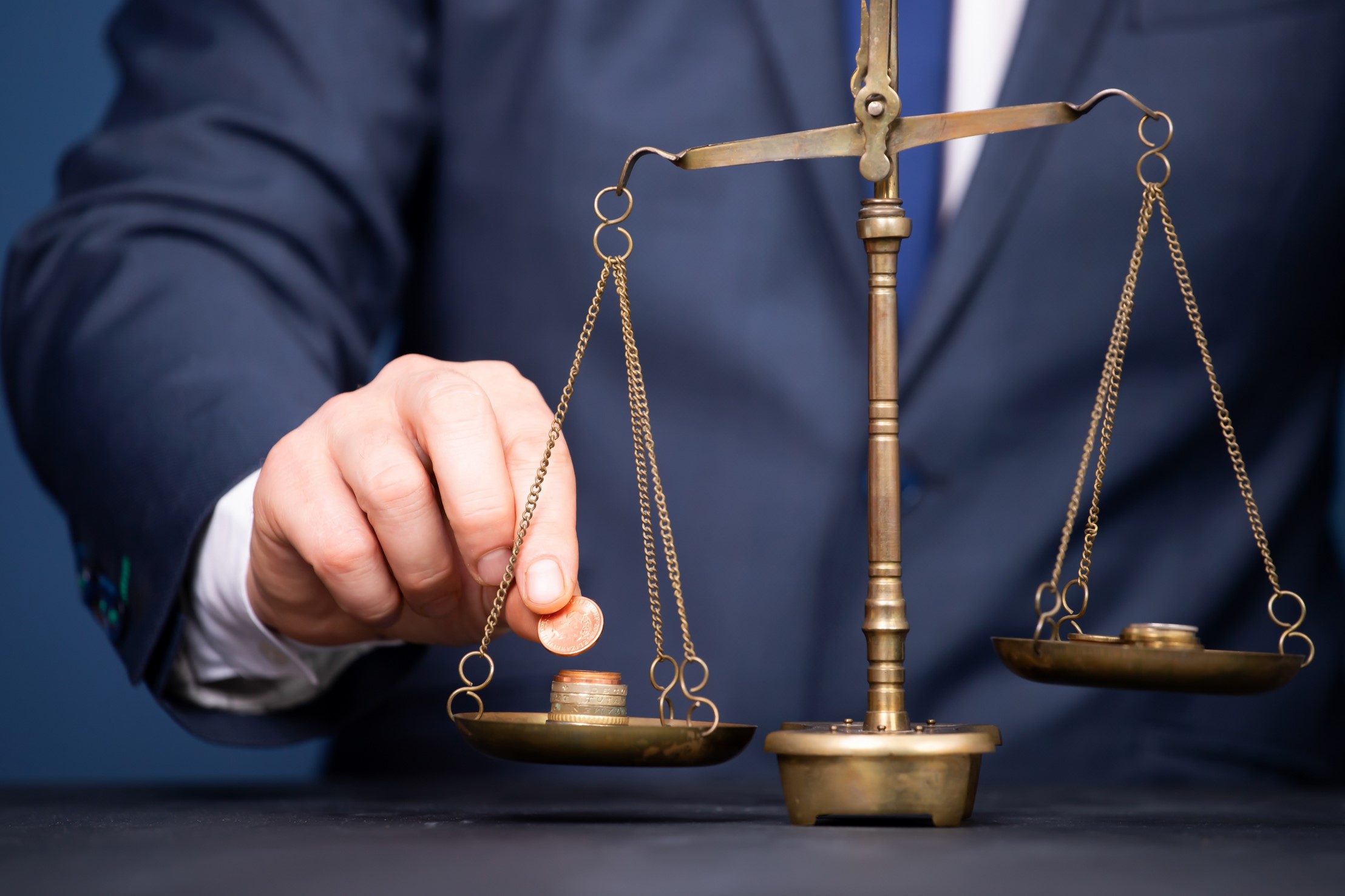
A step-by-step transformation to Industry 4.0 requires a holistic approach in four dimensions:
- Resources
- Information systems
- Culture
- Organizational structure
To successfully drive these four dimensions, an organization needs to equally invest in them. An imbalance leads to missed I4.0 potential and restricts the growth of the organization. An unbalanced investment can be in the form of a lack of infrastructural/technological upgrades, inadequate training of employees, hierarchical silos, etc.
These investments do not seem like a necessity when you are testing a pilot project at a specific machine or line. Small investments at first seem to have a big impact, so the temptation to simply continue by adding additional low-cost pilots is always there. However, this leads to fragmented island solutions which do not give the desired value as they are not implemented end-to-end. Technologies sometimes are implemented in fragments over the process chain. This incomplete implementation then does not give the expected results.
A classic example that we can talk about is traceability. For traceability, products, jigs or material carriers are equipped with barcodes or QR codes. There are certain processes such as coating where it becomes technologically challenging to implement barcodes or QR codes. However, when a process is skipped in building the traceability, and there are no other considerations taken which ensure that even without sensors it is possible to keep up the traceability chain, the whole purpose of the traceability is lost. Material cannot be traced over the “gap” anymore, and neither can process or quality parameters. A holistic view ensuring a process that works with traceability, by for example ensuring a FIFO or one-piece-flow operation, preventing swapping or removing of items from the line by operators unless this is registered, etc. would be needed to keep the benefits.
.png)
Since the technology often is not implemented thoroughly, it can at most be used to help with continuous local improvement. The data collected in this process is not complete and does not help to give the right information about what is happening on the shop floor. If the data is incomplete, traceability throughout the whole process would not be possible. This means that the end-to-end operation benefit which has been hoped for does not materialize – all because of singular gaps in the data flow.
Moreover, if you use this data as a basis for your KPI dashboard, the visualizations will be incorrect. A nice-looking dashboard will not help decision making if the data base is not complete. Nevertheless, the application of these dashboards only makes sense, if the whole process chain is equipped with sensor technologies that constantly generate a reliable database without gaps.
To avoid these pitfalls, it is important to understand that a pilot is just that – a pilot. Adding more of these on top of each other is not a replacement for a strategically defined and analysed set of capabilities that are implemented consistently. Focusing too much on easy wins results in overengineered solutions e.g. at new machines, but without at least a baseline of transparency over the whole value stream this is unlikely to give transformative benefits. In the end it is not different to any other major value stream optimizations – it is fine to try locally and harvest small improvements, but then a good analysis is needed for an end-to-end improvement. And it is not enough to throw technology at the problem, the mindset of thinking about digitalization is also important.
We can support you through your digital transformation process and help you make the right investment decisions.
Let's connect!
Get in touch with us for further information!
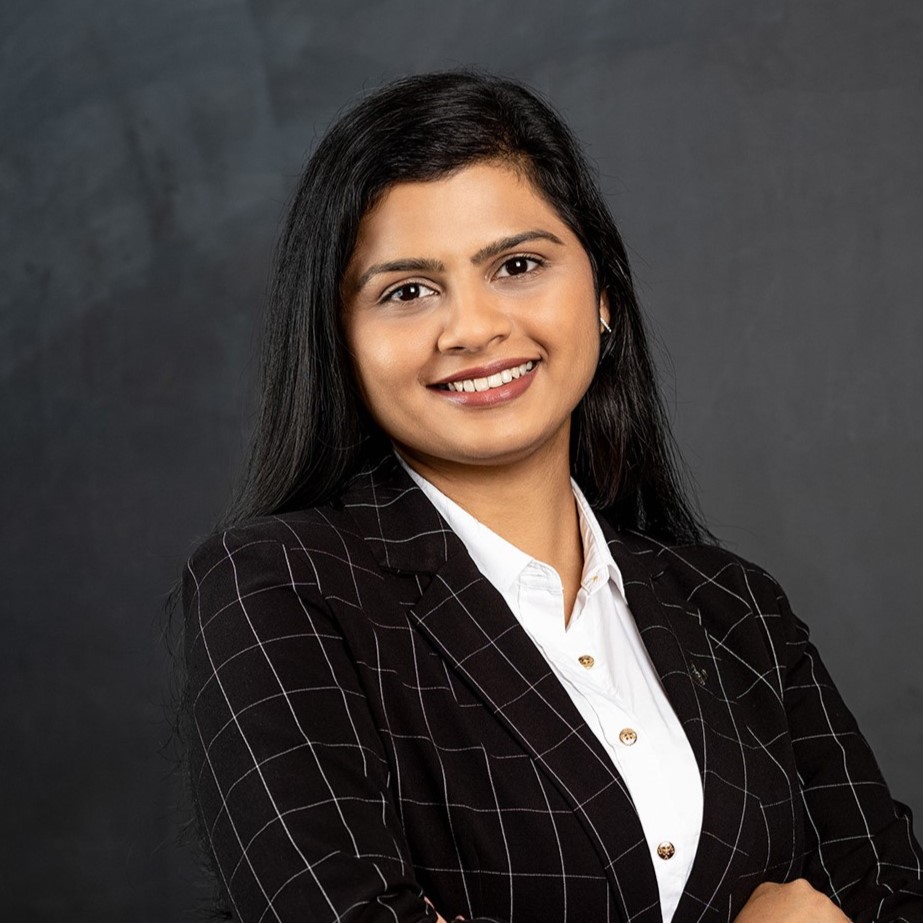
Subscribe to receive the latest insights directly to your inbox.